Infrared and
thermal testing
Infrared and
thermal testing is
one of many nondestructive testing techniques designated by the American
Society for Nondestructive Testing (ASNT). Infrared thermography
is the science of measuring and mapping surface temperatures.
"Infrared
thermography, a nondestructive, remote sensing technique, has proved to be an
effective, convenient, and economical method of testing concrete. It can detect
internal voids, delaminations, and cracks in concrete structures such as bridge decks, highway pavements,
garage floors, parking lot pavements, and building walls. As a testing
technique, some of its most important qualities are that (1) it is accurate;
(2) it is repeatable; (3) it need not inconvenience the public; and (4) it is
economical."
An infrared
thermographic scanning system can measure and view temperature patterns based
upon temperature differences as small as a few hundredths of a degree Celsius.
Infrared thermographic testing may be performed during day or night, depending
on environmental conditions and the desired results.
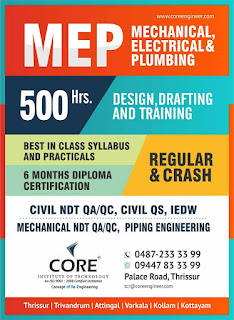
All objects emit electromagnetic radiation of a wavelength dependent on the object's temperature. The frequency of the radiation is inversely proportional to the temperature. In infrared thermography, the radiation is detected and measured with infrared imagers (radiometers). The imagers contain an infrared detector that converts the emitting radiation into electrical signals that are displayed on a color or black and white computer display monitor.
A typical application for regularly available IR Thermographic equipment is looking for "hot spots" in electrical equipment, which illustrates high resistance areas in electrical circuits. These “hot spots” are usually measured in the range of 40 °C to 150 °C (70 to 270 °F) above ambient temperatures. But, when engineers use its patented proprietary systems to locate subsurface targets such as underground storage tanks (USTs), pipelines, pipeline leaks and their plumes, and in this project, hidden tunnels, we are looking for temperature patterns typically in the range of 0.01 °C to 1 °C above or below ambient temperatures.
After the thermal data is processed, it can be displayed on a monitor in multiple shades of gray scale or color. The colors displayed on the thermogram are arbitrarily set by the Thermographer to best illustrate the infrared data being analyzed.
In this roofing investigation application, infrared thermographic data was collected during daytime hours, on both sunny and rainy days. This data collection time allowed for solar heating of the roof, and any entrapped water within the roofing system, during the daylight hours. IR data was observed until the roof had sufficiently warmed to allow detection of the entrapped wet areas because of their ability to collect and store more heat than the dry insulated areas. The wet areas would also transfer the heat at a faster rate than the dry insulated roof areas. At this point in time, the wet areas showed up as warmer roof surface temperatures than the surrounding dry background areas of the roof. During the rainy day, with minimum solar loading, any entrapped leak plumes would become evident because of their cooler temperature as compared to the dry roof areas
An infrared
thermographic scanning system measures surface temperatures only. But the
surface temperatures that are measured on the surface of the ground, above a
buried pipeline, are, to a great extent, dependent upon the subsurface
conditions.
The subsurface
configuration effects are based upon the theory that energy cannot be stopped
from flowing from warmer to cooler areas, it can only be slowed down by the
insulating effects of the material through which it is flowing. Various types
of construction materials have different insulating abilities. In addition,
differing types of pipeline defects have different insulating values.
Contents
- 1Background
- 2Pipeline testing
Background
There are three
ways of transferring energy: 1) conduction; 2) convection; and
3) radiation. Good solid backfill should have the least resistance to
conduction of energy and the convection gas radiation effects should be
negligible. The various types of problems associated with soil erosion and poor
backfill surrounding buried pipelines increase the insulating ability of the
soil, by reducing the energy conduction properties, without substantially
increasing the convection effects. This is because dead air spaces do not allow
the formation of convection currents.
In order to have
an energy flow, there must be an energy source. Since buried pipeline testing
can involve large areas, the heat source has to be low cost and able to give
the ground surface above the pipeline an even distribution of heat. The sun
fulfills both of these requirements. The ground surface reacts, storing or
transmitting the energy received.
Pipeline testing
For pipelines carrying
fluids at temperatures above or below the ambient ground temperatures (i.e.,
steam, oil, liquefied gases, or chemicals), an alternative is to use the heat
sinking ability of the earth to draw heat from the pipeline under test. The
crucial point to remember is that the energy must be flowing through the ground
and fluids.
Ground cover must
be evaluated for temperature differentials (i.e., anomalies such as high grass
or surface debris), as to how it may affect the surface condition of the test
area. Of the three methods of energy transfer, radiation is the method that has
the most profound effect upon the ability of the surface to transfer energy.
The ability of a material to radiate energy is measured by the emissivity of
the material. This is defined as the ability of the material to release energy
as compared to a perfect blackbody radiator. This is strictly a surface
property. It normally exhibits itself in higher values for rough surfaces and
lower values for smooth surfaces. For example, rough concrete may have an
emissivity of 0.95 while a shiny piece of tinfoil may have an emissivity of
only 0.05. In practical terms, this means that when looking at large areas of
ground cover, the engineer in charge of testing must be aware of differing
surface textures caused by such things as broom roughed spots, tire rubber
tracks, oil spots, loose sand and dirt on the surface and the height of grassy
areas
No comments:
Post a Comment