DAILY SCIENCE
Tuesday, 3 March 2020
Air Duct Contaminants in HVAC System
Air Ducts Contaminants Commonly Found in HVAC Systems
Air Ducts Living Particles
How Do I Know if My Air Ducts Need to Be Cleaned?
Major Benefits of Cleaning Your Air Ducts
A Cleaner Smelling Home
Fewer Allergens
Improves Efficiency
Protecting Your Home
Friday, 14 February 2020
DESTRUCTIVE TESTING
Destructive
testing
In destructive
testing (or destructive physical analysis, DPA)
tests are carried out to the specimen's failure, in order to understand a
specimen's performance or material behavior under different loads. These tests
are generally much easier to carry out, yield more information, and are easier
to interpret than nondestructive testing. Destructive testing is most
suitable, and economic, for objects which will be mass-produced, as the
cost of destroying a small number of specimens is negligible. It is usually not
economical to do destructive testing where only one or very few items are to be
produced (for example, in the case of a building). Analyzing and documenting
the destructive failure mode is often accomplished using a high-speed camera recording
continuously (movie-loop) until the failure is detected. Detecting the failure
can be accomplished using a sound detector or stress gauge which produces a
signal to trigger the high-speed camera. These high-speed cameras have advanced
recording modes to capture almost any type of destructive failure. After
the failure the high-speed camera will stop recording. The captured images can
be played back in slow motion showing precisely what happens before,
during and after the destructive event, image by image.
Contents
- 1Methods and techniques
- 1.1Testing of large structures
- 1.2Software testing
- 2Automotive testing
- 3Aircraft testing
- 4See also
Methods and
techniques
Testing of
large structures
Snapshot
from shake-table video of a 6-story non-ductile concrete building
Building
structures or large nonbuilding structures (such as dams and
bridges) are rarely subjected to destructive testing due to the prohibitive
cost of constructing a building, or a scale model of a building, just to
destroy it.
Earthquake
engineering requires a good understanding of how structures will perform
at earthquakes. Destructive tests are more frequently carried out for
structures which are to be constructed in earthquake zones. Such tests are
sometimes referred to as crash tests, and they are carried out to
verify the designed seismic performance of a new building, or the
actual performance of an existing building. The tests are, mostly, carried out
on a platform called a shake-table which is designed to shake in the
same manner as an earthquake. Results of those tests often include the
corresponding shake-table videos.
Testing of
structures in earthquakes is increasingly done by modelling the structure using
specialist finite element software.
Software
testing
Destructive
software testing is a type of software testing which attempts to
cause a piece of software to fail in an uncontrolled manner, in order to test
its robustness and to help establish range limits, within which the SW will operate
in a stable and reliable manner.
Automotive
testing
Oblique
frontal crash test of a Dodge Dart.
Automobiles are
subject to crash testing by both automobile manufactures and a
variety of agencies.
Aircraft testing
Further
information: Aviation safety
NASA air safety
experiment Controlled Impact Demonstration. The airplane is a Boeing
720 testing a form of jet fuel, known as "antimisting kerosene",
which formed a difficult-to-ignite gel when agitated violently, as in a crash.
There has also
been extensive destructive testing of passenger and military aircraft,
conducted by aircraft manufacturers and organizations like NASA.
The 2012 Boeing 727 crash experiment was conducted and filmed by
the Discovery channel.
See also
- Crash test
- Hardness tests
- Median lethal dose
- Metallographic test
- Nondestructive testing
- Reproducibility
- Show and Display
- Stress tests
- Testability
Wednesday, 12 February 2020
TOP 5 BEST NEW FEATURES IN REVIT 2020.2
TOP 5 BEST NEW FEATURES IN REVIT 2020.2
1- MARKER FOR INTERNAL ORIGIN
Activate the visibility of the Internal
Origin under the Site category in the Visiblity/Graphics menu.

arrow represents left-right (x-axis) and the green arrow represents bottom-up (y-axis).
Don’t forget: the
internal origin cannot be moved. When you start a project, make sure you model
in relation to this marker. Usually, it should be located at the intersection
of important grids.
Revit control interface inside
perspective views has always been horrible. If you want to explore a model,
your best option is to export to Enscape or Lumion. Using WASD keys to move
like in a first-person shooter game is much more intuitive than using Revit’s
awful navigation wheel.
Maybe Autodesk are reading this blog?
I complained about the terrible 3D control in the in the 2019.1 update review.
With 2020.2, they are now introducing the Fly mode. This can be
activated inside a perspective view. Click on the small paper plane icon in the
Navigation Bar.
Activating this feature will create
an experience similar to Enscape and Lumion. You can use WASD keys to
move. Q and E keys can be used to move up and down. Use Shift
+ Mouse Wheel to adjust the spot while moving through the view. The control
are good, but it would be nice to have the option to toggle between Walk and
Fly like you can in Enscape. In the image below, you can see how the tool is
used to move and pan around the project.
3-
PATH OF TRAVEL ADD AND EDIT WAYPOINTS

You now have the ability to manually
add intermediate points on the travel path. When the Path of Travel line is
selected, the Add Waypoint and Delete Waypoint tools will appear
in the contextual tab.
Select the Add Waypoint tool
and click on the path of travel. Drag the point to adjust. The path of travel
will automatically adjust.
If you change your mind, you can
remove the point. Select Delete Waypoint and click on the point.
4-
FREEZE HEADER IN SCHEDULE
If you have long schedules in which
you have to scroll down a lot, the headers won’t be visible. In the new update,
you can click on Freeze
Header in the contextual tab. The headers will
be displayed on the schedule even if you are scrolled down all the way to the
bottom.

5-
HIGHLIGHT ACTIVE ROW IN SCHEDULE
A small but appreciated change: the
selected row will now be highlighted in a light blue color.
OTHER CHANGES:
·
Dynamo 2.3 has been released.
·
New Dynamo nodes for steel
connections.
·
Edit circuits and panels in panel
schedule.
Wednesday, 8 January 2020
Fusion 360
Fusion 360
Fusion 360 is a new tool from Autodesk that is taking the 3D
world by storm. The tool lowers the barrier for entry into CAD software, making
it a great way to utilise the precision modelling tools that CAD tools offer,
which can then be exported to any 3d modelling software for the advanced
texture and animation capabilities that they provide.
Thanks to
Fusion 360’s straightforward spline and modelling tools, along with an
excellent model history paradigm, an artist new to CAD software will find their
feet quickly (for more on why Fusion 360 is so innovative, jump to the section
on the different between Cad and 3D software).

Fusion 360 is
available as a free product if being used by a student, and has a similar cost
per year compared to many of the tools a 3D artist uses from day to day when
using it professionally. Let’s take a closer look at the tools of features on
offer.
01. Model in Fusion 360

02. Modify a spline and Extrude
The corners of a spline
are easily modified using the Fillet tool. When happy with the shape of the
line, it can be easily extruded using the Extrude function to a set dimension.
When the extrude is complete, another spline can then be created – for example,
a circle that can be used as a cutting object when it is extruded into the
initial extruded shape. This technique allows the creation of complex objects
in seconds.
03. Use the History timeline
The history timeline is a
series of icons at the bottom left of the screen showing each creation stage of
the modelling process. The timeline can be moved back in time to allow you to
modify your design. In the example shown, the original spline has had an offset
applied to it to allow the hollowing out of the initial shape via an extrude. The
history timeline is a great way to both ensure changes are easy to manage and
new designs are easily branched off.
04. Export to a 3D application
To enable the export
options available in Fusion 360, the model needs to be saved to the Autodesk
cloud. From here, a wide range of file types are available for export. FBX is
an excellent format that can be used in a wide range of 3D packages, while also
retaining a lot of the detail. It is best to experiment with a variety of
different formats, as Fusion 360 makes subtle changes to the geometry dependent
on the format used.
05. Explore the interface
Friday, 3 January 2020
Electromagnetic testing
Electromagnetic testing
Electromagnetic testing (ET), as a form
of nondestructive testing, is the process of inducing electric
currents or magnetic fields or both inside a test object and
observing the electromagnetic response. If the test is set up properly,
a defect inside the test object creates a measurable response.
The term "electromagnetic testing" is often
intended to mean simply eddy-current testing (ECT). However, with an
expanding number of electromagnetic and magnetic test methods, "electromagnetic
testing" is more often used to mean the whole class of electromagnetic
test methods, of which eddy-current testing is just one. also useful for the
testing of drill pipes.
Common methods
- Eddy-current
testing (ECT) is used to detect near-surface cracks and corrosion in
metallic objects such as tubes and aircraft fuselage and structures. ECT
is more commonly applied to nonferromagnetic materials, since
in ferromagnetic materials the depth of penetration is
relatively small.
- Remote
field testing (RFT) is used for nondestructive testing (NDT) of steel
tubes and pipes.
- Magnetic
flux leakage testing (MFL) is also used for nondestructive testing
(NDT) of steel tubes and pipes. At present RFT is more commonly used in
small diameter tubes and MFL in larger diameter pipes over long travel
distances.
- Wire
rope testing is MFL applied to steel cables, to detect broken strands
of wire.
- Magnetic
particle inspection (MT or MPI) is a form of MFL where small magnetic
particles in the form of a powder or liquid are sprayed on the magnetized
steel test object and gather at surface-breaking cracks.
- Alternating
current field measurement (ACFM) is similar to eddy current applied
to steel. Its most common application is to detect and size cracks in
welds. from the company that developed it.
- Pulsed
eddy current enables the detection of large-volume metal loss in
steel objects from a considerable stand-off, allowing steel pipes to be
tested without removing insulation.
See also
- Electromagnetic
compatibility
Friday, 27 December 2019
HVAC System Maintenance Tips
HVAC System Maintenance: 6 Tips for Hot Season
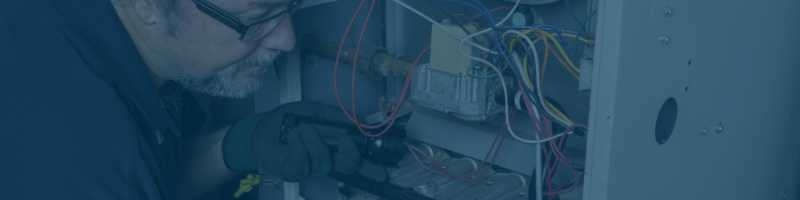
As a building or property manager, it’s your job to maintain a safe and comfortable environment for everyone working or living in the building. The quickest way to get people complaining is to mess with the temperature.
Don’t leave your tenants out in the cold. Instead, be proactive and make sure your HVAC system is properly maintained. Your reputation depends on people knowing they can rely on you to keep the building running smoothly.
Also, it’s easier to fix problems before they become emergencies. This season, make HVAC system maintenance a priority so you can be sure your heating will keep working when you need it most.
6 essential HVAC system maintenance tasks for heating equipment
1. Clean or replace air filters


Clogged filters can also result in more dust and pollen in the air, which can worsen health conditions for people with asthma and allergies. Plus, more dust and debris gets into your equipment and can cause damage over time.
2. Have the ventilation system checked
The ductwork that moves heated air throughout the building, and the flues that vent exhaust out, are the most overlooked parts of the HVAC system. Don’t let it be out of sight, out of mind. Have an expert check the ducts and vents for any dislocated parts, clogs, holes, or corrosion, so you can correct any problems that impact your comfort conditions (and energy usage).

Ductwork repair might seem like an easy enough task to tackle yourself, but it’s not recommended. Many DIY repair attempts end up damaging the equipment. Get a professional HVAC tech in to assess and repair a structural issue or blocked flue.
3. Clean exterior components
When it comes to HVAC system maintenance, your system’s exterior components (such as condensers and rooftop units) need as much attention as your as the interior units. Possibly even more so, as the outdoor units are exposed to the elements.
Make sure to keep outdoor equipment unit clear of leaves and snow, especially after a storm. Pay special attention to the area around the outdoor air intake. This supplies air for the whole system, so if there’s any blockage or source of contamination nearby, this can affect the air in the whole building. It’s recommended to maintain at least a two foot clearance from the intake valve.
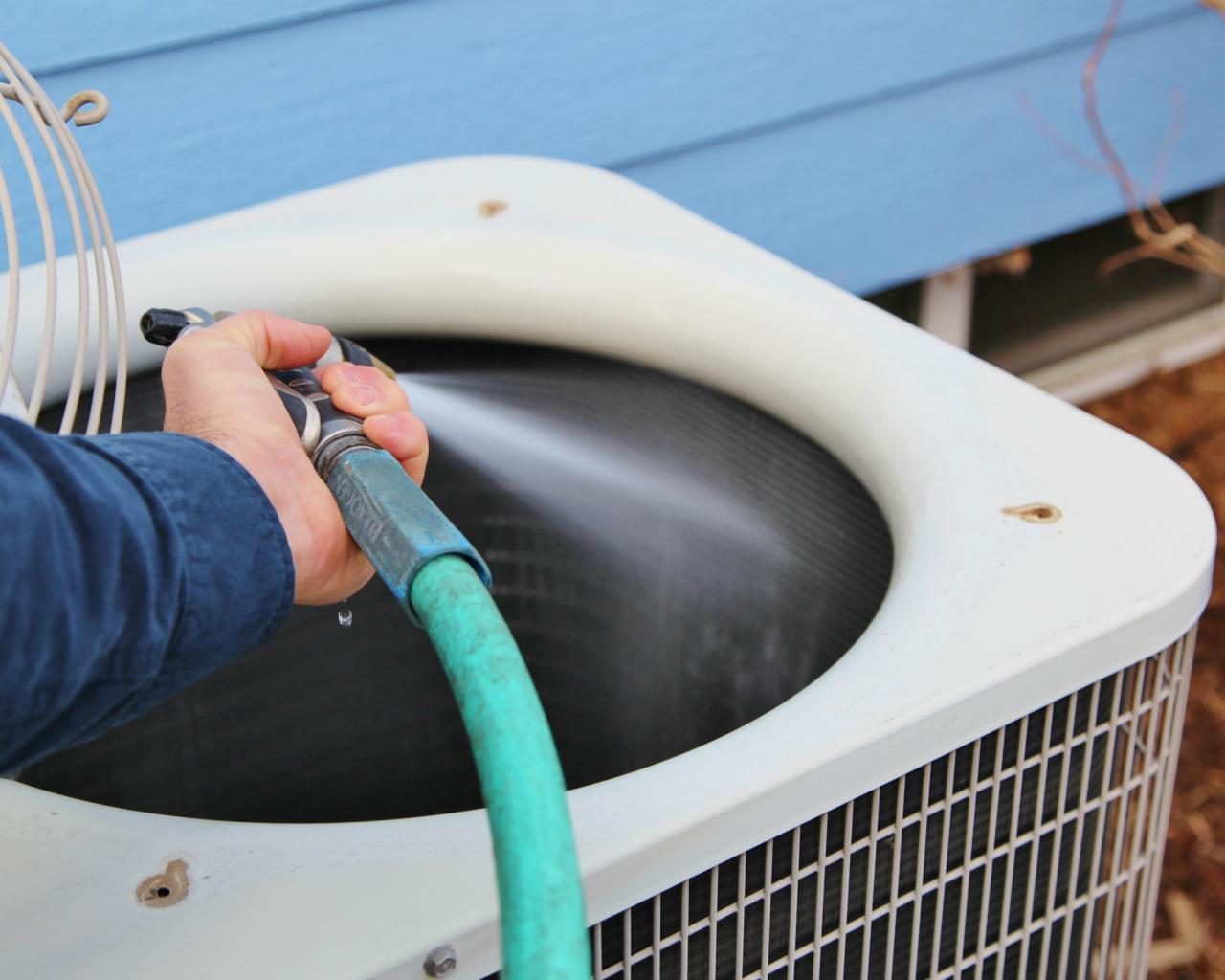
Your HVAC maintenance plan should include cleaning outdoor components at least a couple of times each year. The coils, motors, and fan blades operate more efficiently when cleaned.
4. Keep an eye out for mold
Where there is moisture, there is the potential for mold to grow. To prevent mold, keep an eye out for any signs of moisture where it doesn’t belong. It can be difficult to get rid of, not to mention the potential health hazards for the people in your building.

A good HVAC system maintenance plan will focus on inspecting the most common places where moisture can build up. These include boilers, ventilation shafts, coils, drain lines, and drain pans.
5. Replace worn parts proactively
HVAC system maintenance should always include inspections of your system’s condition and identification of aging parts. Replacing worn parts BEFORE they break is the best way to prevent breakdowns and expensive repairs.
One critical heating component to pay attention to is the ignition assembly. This is a delicate part of the furnace that, if dirty or damaged, will leave you without any heat. Replacing fan belts when they show wear also helps prevent breakdowns and helps your equipment operate efficiently.
6. Keep an HVAC system maintenance calendar & get a maintenance contract
HVAC is a complex system with many components. Especially for a large commercial or base building system, the number of pieces to keep track of can really add up.
Subscribe to:
Posts (Atom)